Capabilities
- Listen and understand the customer’s needs.
- Discuss and provide professional and flexible packaging solutions.
- Introduce the suitable packaging machine based on customer’s products.
- Visit customer’s plant and measure the space to fit the machine in.
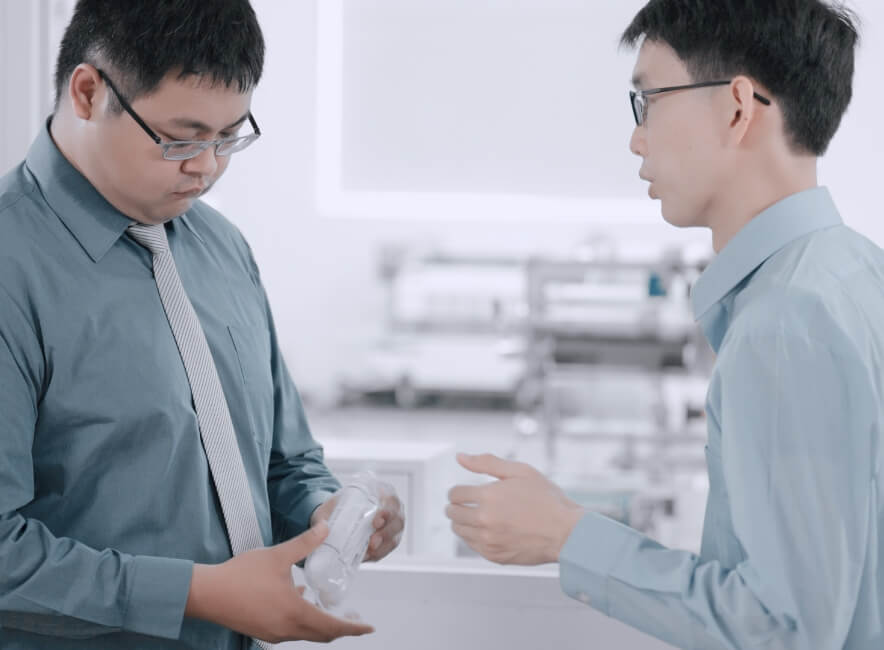
- We utilize professional 3D design software that allows us to simulate and draw various packaging structures.
- Continuously evolve the research and development in packaging industry.
- Repeatedly make improvement of packaging machines.
- Develop various models from entry to advanced types, applying with servo controls.
- Challenge and pursue high speed packaging, reduce the consumption of films, save the labor cost.
- Plan fully automatic packaging lines, along with robotic arms, conveyors, or boxing even palletizing.
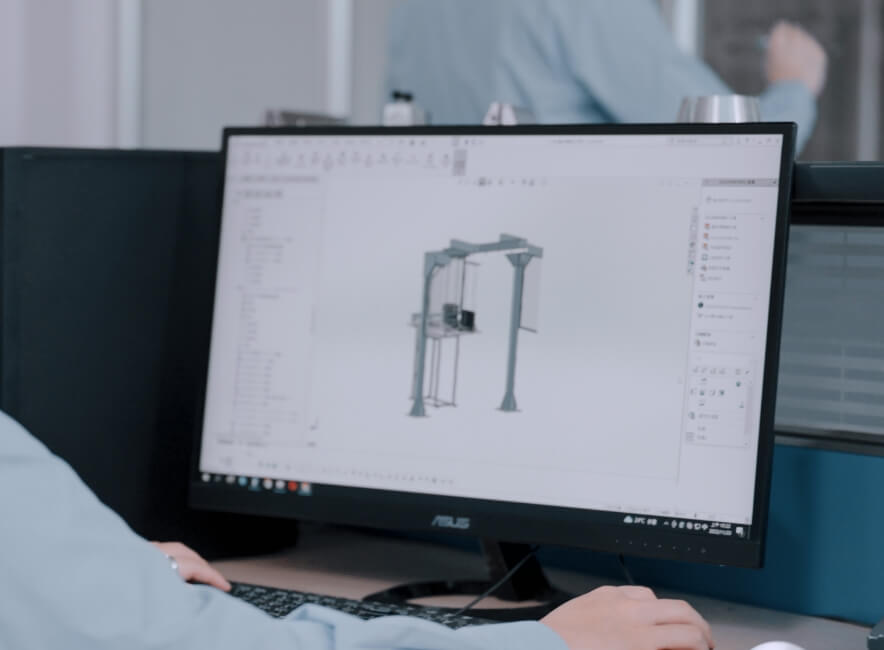
We utilize professional 3D design software that enables us to simulate and draw new packaging equipment structures. Through this software, we can create virtual models and prototypes, allowing us to visualize and assess the feasibility and functionality of the designs before proceeding with physical production.
The 3D design software empowers our engineering team to explore various design concepts and configurations, optimizing the equipment's performance and efficiency. This approach saves time and resources by identifying potential issues or improvements early in the development phase.
Moreover, the software's advanced simulation capabilities enable us to conduct stress tests, evaluate material properties, and analyze the equipment's behavior under different operating conditions. This data-driven approach helps us ensure the structural integrity and durability of the new packaging equipment.
By leveraging 3D design software, we enhance the innovation and precision of our packaging equipment development process. It allows us to tailor solutions according to specific customer requirements, accelerating the design-to-production timeline and delivering cutting-edge packaging solutions to meet the evolving needs of the industry.
- Have solid and stable technical capabilities.
- Full and precise processing tools to make the structure sturdy.
- We employ multiple high-precision measuring devices to inspect the assembly quality.
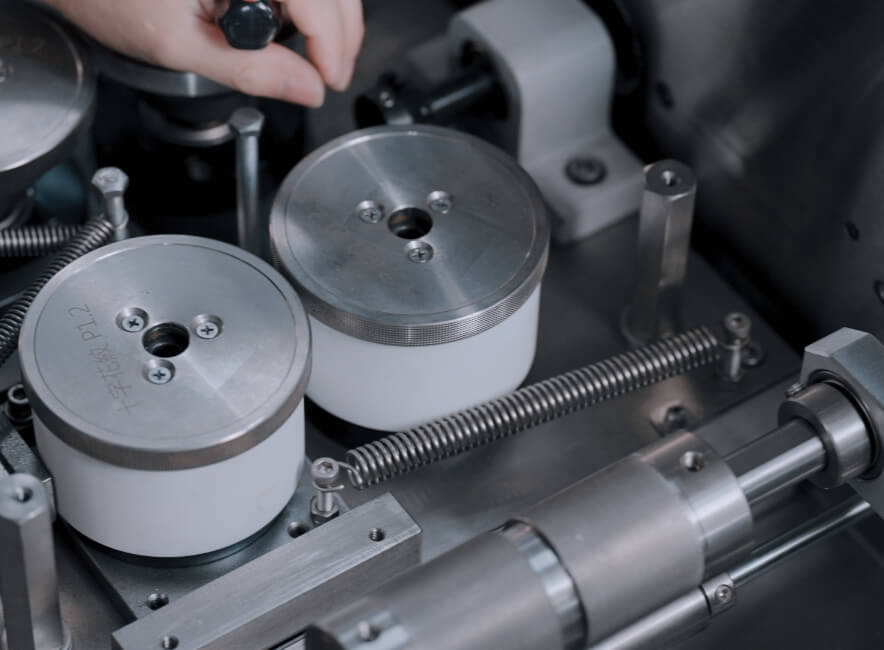
We use comprehensive and precise processing tools to ensure the structural robustness. We are committed to delivering excellent assembly quality, and thus, we carefully select a variety of high-quality tools during the production process to ensure accurate fitting and sturdy connections for each component.
These processing tools encompass various types and sizes, catering to different assembly requirements. Our skilled technical team possesses vast experience and can flexibly choose and apply the appropriate tools based on design specifications and customer demands. Whether traditional manual tools or advanced automated equipment, we continually update and optimize our tool inventory to ensure the efficiency and accuracy of the assembly process.
Each tool undergoes rigorous calibration and maintenance to maintain its high precision and reliability. We prioritize quality control, ensuring that every step of the process adheres to strict standards and specifications. By using high-quality tools, we can guarantee the assembly quality of our products and minimize potential errors and defects during production.
During the assembly process, we also focus on training our staff to proficiently use various tools correctly. This enhances production efficiency and reduces potential issues caused by human factors. We believe that with advanced tools and a highly skilled team, we can provide customers with high-quality and reliable assembly services, meeting their stringent demands for product quality.
- Run the trial test and set all the product information in the software before delivery.
- Concentrate on machine’s operability and maintainability to achieve high quality and make operating easier.
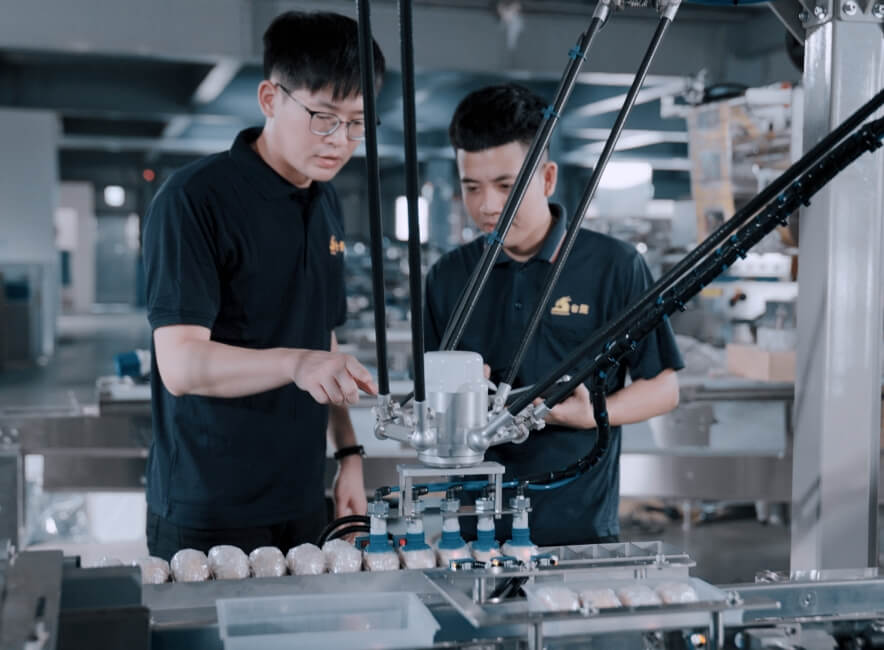
Before delivery, we will conduct trial tests and set all the product information in the software.
After the production is completed, we will perform trial tests to ensure the proper functioning and performance of the packaging equipment. Through the trial run, we can inspect various functions and components of the equipment, ensuring that it meets design requirements, and adjust any necessary parameters.
Additionally, before delivery, we will set all the product information in the software. This includes technical specifications, operating parameters, safety requirements, and other relevant details. Integrating product information into the software enables convenient operation and management, while ensuring that customers have access to accurate information and data when using the equipment.
By conducting trial tests and setting product information in the software, we are committed to providing high-quality and efficient packaging equipment that meets customer requirements and ensures a smooth integration of the equipment into production and operations.